Introduction
Metal matrix composites are materials that are combining the toughness of metals with in most cases the high intrinsic strength and stiffness of ceramics. The strengthening material can be used in a wide range of shape (rod, foil, short or long fibre, sphere, etc...) and size. Such materials provide the most beneficial specific strength and stiffness. However the forming process has to be treated as a case by case basis. Like for other kinds of materials this comes from the interaction between forming process, the produced material and its ensuing properties. This is related to parameters such as temperature, pressure, chemical potentials of species, time, activation energy, viscosity, etc... Although in composites we also have to consider the interaction between the composites materials themselves during the forming progression. This aspect makes the study of forming and characterization of composite materials a broken up branch and outperforms the simple learning of separated materials involved in composites.
Material |
sy(MPa) |
r (kg/m³) |
E (GPa) |
d (10-3 MPa.m³/kg) |
q (10-3 GPa.m³/kg) |
AISI 314 (annealed) |
320-360 |
7800-8000 |
195-200 |
40-46 |
24-26 |
TA6V |
780-910 |
4430-4510 |
110-119 |
170-210 |
24-27 |
BFR-Al (50%) |
910-925 |
2700-2710 |
208-215 |
330-340 |
77-80 |
CFR-Mg (70%) |
650-660 |
1790-1860 |
91-93 |
350-370 |
49-52 |
Comparison between AISI314 and TA6V alloys and boron fibres and carbon fibres reinforced matrixes. MMC exhibit a higher specific strength and stiffness.
Facilities of MMS unit
In order to ease the study of MMC several equipments are available at MMS. They are helpful for manufacturing and characterization.
EVA Machine: This makes possible the cold coating of reinforcement material (such as fibres weave) by a pure metal (Al, Zr, Ti, Mg, Zn, Cu, etc ...) as a pre-treatment in order to control or even to prevent an interfacial phenomena during a next hot process such as heating, melting or thixoforming.
Vacuum oven: We are able to heat materials from ambient temperature to 1600 °C under a vacuum atmosphere. Such a treatment is supportive to minimize the effect of air or other gas by lowering their partial pressure in various experimental conditions. For example the interaction between reinforcement materials covered by a PVD layer is pointed out thanks to heat treatment under a vacuum atmosphere. This is particularly interesting for materials with a high specific area such powders of fibres.
Electronic microscopy: For microscopic characterization of products or semi-products MMS unit is partnered with CATµ support unit inside University of Liege. We are able to identify metallurgical phases or particular species with a high order of magnification and we have the possibility to spot the chemical composition (EDX).
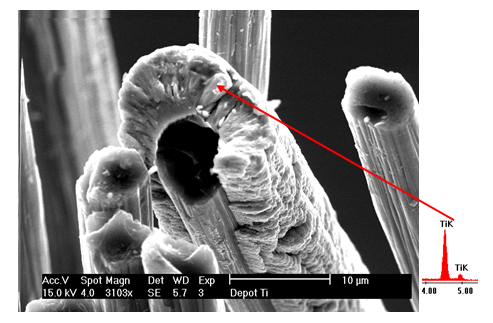
View of a Ti coated fibre for MMC composite with EDX spectrum
DTA/DSC: In order to show chemical affinity between matrix and reinforcement, DTA or DSC techniques can be used. The principle is to heat a sample and compare the quantity of stored heat with an inert reference. The most important parameter is the sensitivity of such devices in order to detect the heat of chemical reaction in the sample. It is particularly difficult when the reactive volume is low as in interfacial reactions.
Research
· Al + SiC: Aluminium matrix (2024 & 319) were reinforced by 10% of SiC short fibres. The manufacturing process was stir casting. The results exhibit a gain of 10-15% of yield strength of 2024 matrix at 20 °C and 250 °C compared to unreinforced matrix. Al 319 matrix doesn’t give a significant increase of strength because a reaction between fibres and liquid matrix occurs.
· Mg + C: This project concerns the forming of a carbon fibre reinforced magnesium plate by the thixoforming process. The research period is comprised between oct. 2008 and oct. 2011. This is a multi-disciplinary challenge :
o We have to use long carbon fibre weaves (set in mould before injection).
o The wetability has to be high even for short time contacts between weave and alloy.
These aspects are likely to suggest a step by step part manufacturing:
o Fix some selected carbon weave layers
o Agglomerate these layers with aluminium phosphate to make a first stiff part with higher affinity for liquid magnesium
o Set this part in the heated mould of thixoforming machine and proceed with injection
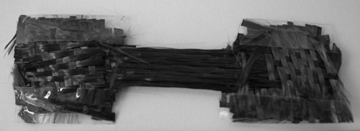
Fixed carbon weaves for upcoming tensile test after injection
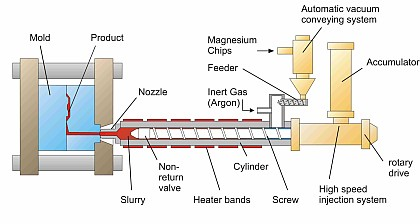
Thixoforming machine (http://www.nmfgmbh.de/)
Previous page: Activité de recherche
Next page: Matériaux pour aéronautique : alliages de titane